The Ultimate Guide to Product Packaging Maker Repair: Keep Your Operations Running Smoothly
Comprehending the complexities of product packaging maker repair work is essential for keeping ideal performance and decreasing interruptions. Regular upkeep not only expands the life of these makers but additionally addresses typical issues that can restrain efficiency.
Importance of Routine Maintenance
Routine maintenance of product packaging machines is critical for making sure optimal performance and longevity. By carrying out a structured maintenance timetable, operators can recognize potential concerns before they intensify right into considerable troubles. This proactive strategy not only lessens downtime yet likewise expands the lifespan of the devices, inevitably resulting in lowered operational expenses.
Regular examinations permit the evaluation of essential components such as seals, sensing units, and belts. Addressing deterioration immediately prevents unexpected failures that might interfere with production and result in expensive repair services. In addition, routine maintenance helps make sure conformity with sector criteria and regulations, cultivating a risk-free functioning setting.
In addition, upkeep activities such as calibration, lubrication, and cleaning considerably improve device effectiveness. Enhanced performance equates to constant product high quality, which is important for preserving consumer contentment and brand credibility. A well-kept packaging device operates at optimal rates and lowers product waste, adding to general efficiency.
Common Packaging Machine Concerns
Product packaging makers, like any type of complex machinery, can run into a selection of typical problems that may prevent their efficiency and effectiveness - packaging machine repair. One prevalent trouble is irregular sealing, which can lead to item wasting and wastage if plans are not appropriately sealed. This frequently arises from misaligned elements or worn securing aspects
Another constant problem is mechanical jams, which can occur as a result of foreign objects, used parts, or inappropriate positioning. Jams can cause hold-ups in production and rise downtime, eventually affecting total productivity. In addition, electronic breakdowns, such as failure in sensing units or control systems, can interrupt procedures and lead to unreliable dimensions or unpredictable machine habits.
Furthermore, problems with item feed can likewise emerge, where items might not be delivered to the packaging location regularly, creating interruptions. Finally, wear and tear on belts and rollers can bring about suboptimal performance, needing prompt attention to protect against further damage.
Understanding these typical problems is essential for maintaining the stability of product packaging procedures, ensuring that machinery runs smoothly and successfully, which subsequently helps in meeting production targets and preserving item top quality.
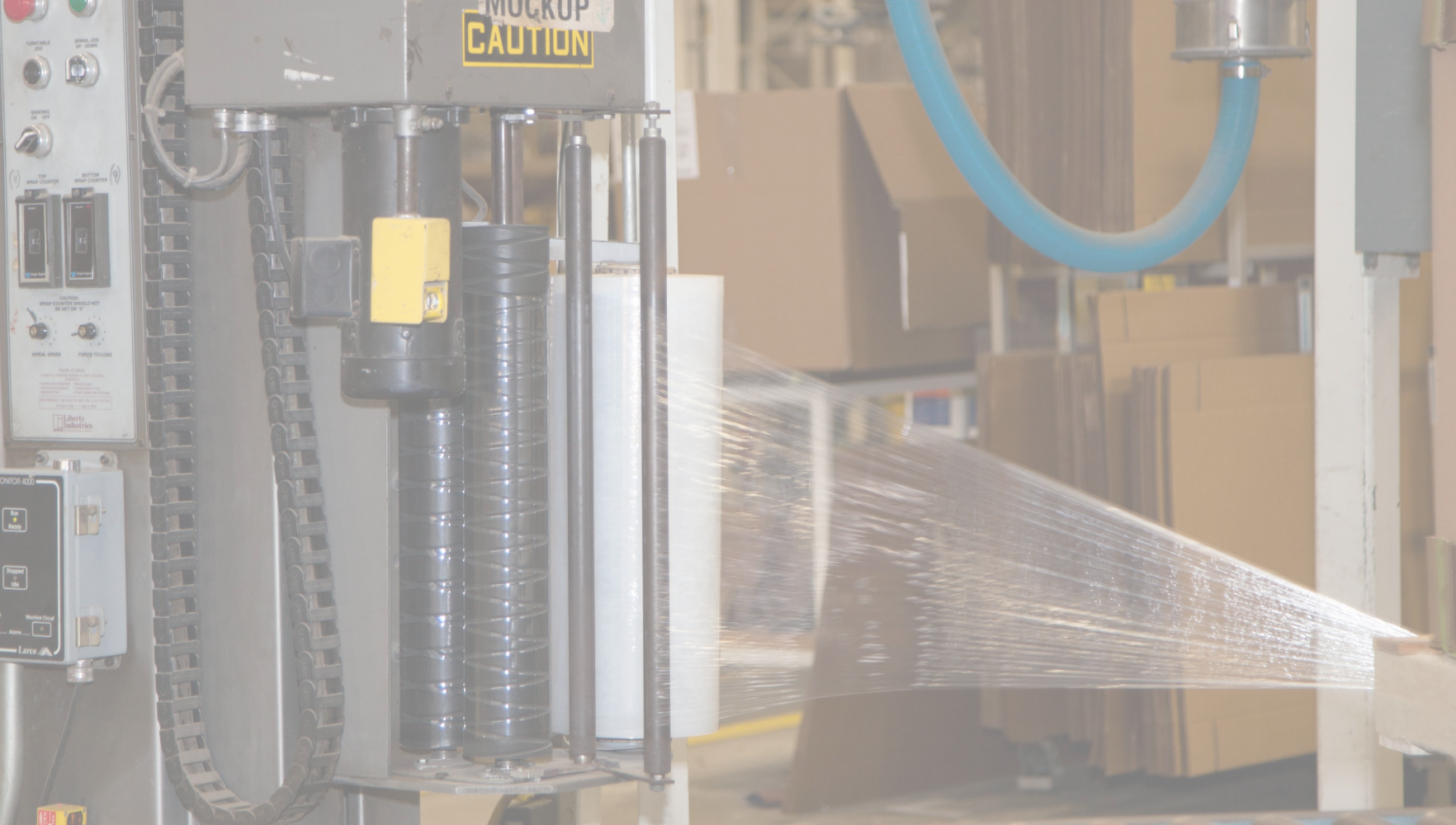
Fixing Techniques
Reliable fixing techniques are crucial for immediately addressing concerns that occur with packaging makers. A systematic strategy is crucial for identifying the origin of breakdowns and minimizing downtime. Begin by collecting information regarding the symptoms observed; this might consist of unusual sounds, operational hold-ups, or mistake codes shown on the maker's interface.
Following, refer to the maker's manual for fixing standards particular to the version concerned. This source can give important understandings into typical problems and advised analysis actions. Make use of aesthetic inspections to check for loose connections, worn belts, or misaligned elements, as these physical elements frequently contribute to operational failures.
Execute a process of elimination by testing individual device features. For example, if a seal is not creating appropriately, examine the securing mechanism and temperature level setups to identify if they satisfy functional requirements. Paper each action taken and the outcomes observed, as this can assist in future repairing initiatives.
Repair vs. Replacement Decisions
When confronted with tools breakdowns, determining whether to fix or change a packaging equipment can be a facility and important option. This decision hinges on several vital variables, consisting of the age of the device, the extent of the damages, and the predicted effect on operational efficiency.
To start with, think about the device's age. Older machines might need more constant repair services, resulting in higher collective expenses that can surpass the financial investment in a new device. Furthermore, assess the extent of the breakdown. Minor concerns can typically be dealt with quickly and economically, whereas comprehensive damages may demand a considerable financial dedication for repairs.
Functional downtime is another critical consideration. Investing in a brand-new machine that provides boosted performance and reliability may be extra sensible if repairing the device will certainly create prolonged delays. Moreover, take into consideration the availability of parts; if replacement elements are difficult ahead by, it might be more tactical to replace the maker totally.
Inevitably, performing a cost-benefit analysis that includes both immediate and long-term implications will certainly aid in making an informed decision that aligns with your operational goals and budgetary restraints. (packaging machine repair)
Preventative Procedures for Durability
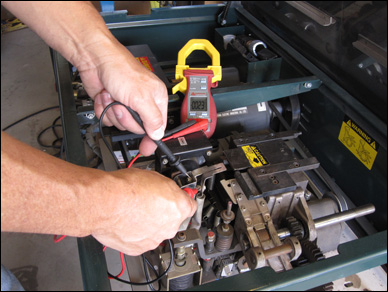
Secret safety nets consist of routine lubrication of moving parts, alignment checks, and calibration of sensors and controls. Developing a cleansing schedule to remove debris and pollutants from machinery can significantly decrease deterioration (packaging machine repair). Furthermore, checking functional criteria such as temperature level and resonance can aid detect irregularities early on
Training team to identify indicators of wear or breakdown is an additional critical blog here part of preventative upkeep. Equipping operators with the understanding to carry out basic troubleshooting can lead to quicker resolutions and minimize functional interruptions.
Documents of upkeep tasks, including service documents and examination searchings for, promotes accountability and facilitates educated decision-making relating to repair services and replacements. By focusing on safety nets, organizations can guarantee their packaging equipments run at peak performance, inevitably causing enhanced productivity and lowered operational costs.
Final Thought
In conclusion, the efficient upkeep and fixing of packaging devices are vital for maintaining functional efficiency. By executing precautionary procedures, organizations can enhance machine durability and make visit site sure nonstop performance in product packaging procedures.
Understanding the intricacies of packaging device repair work is vital for keeping optimum efficiency and decreasing disturbances.Normal upkeep of product packaging equipments is critical for making certain optimum efficiency and long life.Product packaging makers, like any type of complicated machinery, can experience a variety of common issues that might prevent their efficiency and effectiveness. If repairing the machine will create long term hold-ups, investing in a new equipment that supplies improved effectiveness and reliability might be extra sensible.In final thought, the effective upkeep and repair service of packaging machines are paramount for maintaining operational efficiency.
Comments on “How Timely Packaging Machine Repair Can Prevent Costly Downtime”